When looking to expand their reach, fab shops often consider complementary, value-added processes to attract customers and add to their bottom line. Plate rolling is the obvious choice for many shops. The question becomes how to choose the machine that’s the right fit for you.
“Plate rolling machines are one of the most versatile machines in the metal forming industry,” said Andrea Comparin, Faccin Group’s head of sales, Americas. “They can be used to roll metal cans and cones used to manufacture parts and components in a variety of sectors, which maximizes ROI to the fabricating shop easily. The machine can be used to roll and shape a variety of materials, including black steel, stainless steel, high-tensile steels, special steels, and aluminum. It’s just a matter of determining which style of plate roller makes sense for your operations.” Welding Turning Positioner
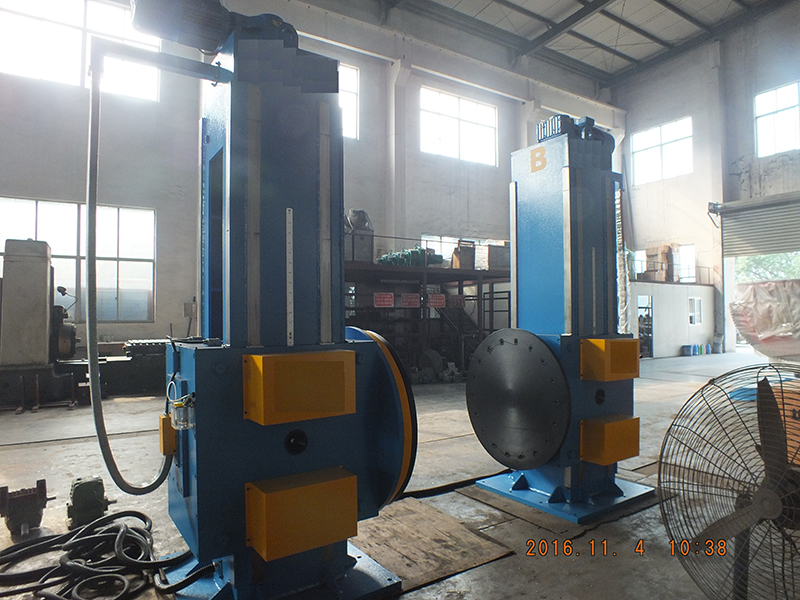
“Almost every shop needs round parts,” said Steve Bonnay, business development manager (Canada) and special projects, DAVI Inc. “At some point, a shop will find that they are outsourcing a significant enough amount to warrant bringing the technology in-house.”
Choosing the right machine configuration will depend on your needs, but ease of use and connectivity are obviously becoming more important as the interconnectivity of the shop becomes critical for production management.
“The plate roller has to be equipped with a user-friendly CNC as well as a remote management system,” said Comparin. “These allow the operator to carry out a wider variety of tasks with greater accuracy while improving productivity.”
As Comparin noted, his company builds two-, three-, and four-roll plate rollers, although most shops are primarily interested in three- and four-roll models.
“The two-roll machines are geared primarily to operations doing large-series production of thin sheet metalwork that is less than 0.2 in., or 5 mm,” he noted. “The three- and four-roll machines are more versatile.”
Pyramid-type plate rolls (with three or four rolls) are divided into two separate categories for cost and performance: bending rolls with planetary guides and bending rolls with linear guides. “The planetary guides are appreciated for their lower cost and the linear guides are preferred because they guarantee a shorter distance between the bending rolls and, therefore, a machine’s rolling precision,” said Comparin.
Four-roll plate rollers tend to be the go-to system unless a shop has specific jobs with special requirements, such as running very heavy plate.
“The four-roll plate bending machines guarantee greater productivity and are easier to use, as well as being the only ones that can effectively be fully automated with numeric controls,” said Comparin. “They are the best solution for those who have to produce pieces in small or large series.”
Here we see light gauge material with a seam being held by an overhead support. DAVI
The automation control comes from the fact that, with a four-roll machine, you always have control of the plate.
“At some point in all three-roll configurations, the material has to be released,” said Bonnay. “The second you release material, there is no way the computer can know where the plate is. For those who use a plasma cutting table, it would be something similar to cutting half a 10- by 20-ft. sheet on your table and then moving the sheet and getting mad at the control when it doesn’t know where the sheet is.
“With a three-roll, because you have to release the material, and in some cases physically take the plate out and spin it around, it does so without the encoder knowing what's going on. It simply won't work. With a four-roll, you take the rear roll (opposite to the side you are loading from) and raise it to the top of its stroke. In that state it acts like a backgauge that you’d find on a press brake. And we know that it is parallel because it is in the machine. It makes it tougher for the operator to make a mistake.”
The four-roll also has a constant pinch.
“The fourth roll is directly underneath the top roll. Its job is to sandwich the material and hold it,” said Bonnay. “That's got two functions. The first one is it lets me put an encoder on it so my CNC can work. But the second function is safety. Even if you're doing a big diameter and there's a 30-ft. plate with 16 ft. sticking out the other side, it is constantly pinched. You don't have to worry about it slipping and falling. On a three-roll, you are wedging it between the rolls, but there is no real constant pinch.”
The four-roll also doesn’t require plate repositioning. You put the plate in, you pinch it, you back up, you prebend, and then you roll in a single pass, assuming you've got the right size machine to roll in a single pass. Meanwhile, all three-roll machines require the plate to be repositioned at some point during the process.
This inevitably means higher productivity on the four-roll setup. Though a four-roll machine may be priced somewhat higher than a three-roll, the control, safety, and related productivity add to its value. They are ideal for repetitive production in an automatic cycle, and are normally used to produce wind towers, truck tanks, HVAC components, etc.
Three-roll machines are preferred for their versatility and flexibility and in turn are divided into two categories: three-roll pyramidal plate rolls (‘linear’ or ‘planetary’) and three-roll plate rolls with variable geometry.
“The three-roll machines are an excellent alternative if there are no requests for mass production,” said Comparin.
The three-roll, pyramid-type, “double-pinch” bending rolls work by aligning or slightly offsetting the top roll with a bottom roll, and the two rolls pinch the material. The third roll then initiates a prebend on the material. Three-roll machines generally require prebending the leading end, then turning the sheet around or running it through the machine to prebend the trailing end, and then switching the roll rotation direction to roll the cylinder body. The top roll is always in a fixed position.
When a machine crowned for thin plate forms heavier material, it can create a concave defect, like a barrel. DAVI
“The challenge with these machines is the space needed on both sides of the machine for prebending both ends of the part,” said Bonnay. “On the plus side, there is no need to remove the material from the machine.
“Single initial-pinch” machines, which have two vertically opposed fixed rolls with a third that is offset, are further hampered by the need to physically turn the sheet around to prebend the trailing edge. For this reason, they are generally only used for light-capacity applications.
“But even if you are just running lighter applications, that’s still two operators required to handle the material, which is always a safety concern,” Bonnay added.
3-roll plate rolls are suitable for versatile and flexible production, including the production of cones. They are normally used to manufacture pressure vessels, heat exchangers, pipelines, etc.
Variable-geometry three-roll plate rolls, meantime, have a top roll that moves up and down while the lower two rolls each move horizontally. This increases the offset distance from the top roll, delivering a distinct mechanical advantage in bending.
“As with any other metal bending machine, the technical feature that characterizes the most bending accuracy is the least possible distance between the points of bending; in a press brake it is the ‘V width,’ in a plate bending roll it is the distance between the rolls,” Comparin explained. “In short, the closer the lateral rolls’ approach to the central axis of the machine, the more precise the rolling will be.”
As an example, Comparin noted that, as in a press brake, the accuracy of rolling means being able to concentrate the bending force on one small portion of sheet metal to obtain a prebend with minimal flat or to optimize the final calibration quality in a longitudinal welded area.
“This is a feature that makes the three-roll variable geometry machine the preferred choice of those fabricators who demand rolling versatility with maximum use of the bending force, precision in prebending and calibration,” he said.
It’s important to know what the maximum and minimum thickness of parts you plan to run on your plate roller will be.
“In a plate roll, like in any other metal forming machine, the bending capacity is directly proportional to the available force,” noted Comparin. “The force required to achieve the bending momentum that forms the steel plate depends directly on the distance (minimum and maximum) between the lateral rolls.
Conversely, if a machine is crowned for a heavy application and is used for thinner plate, it can result in a convex defect, making an hourglass shape. There are various ways to address these deflection issues. DAVI
“In practice, the bigger the distance between the rolls, the smaller the force that they exert because of the leverage effect will that be higher at the expense of circularity tolerances,” Comparin added.
Most shops will automatically consider the thickest and hardest materials they will be processing, but it’s key to know the range expected to understand how to address potential deflection issues.
“No machine will be a perfect fit for every thickness of material, so it’s important when you are talking to suppliers to make sure that your expectations are realistic and that you invest in a system that meets your needs,” said Bonnay. “You need to know the thickest and thinnest material you plan to work with, as well as the smallest diameter you expect to work with, and the widest width you need to work with.”
Deflection is affected by the length of the machine and size of the top roll.
“The longer the machine is and the smaller the top roll, the more that deflection is going to occur,” said Bonnay. “For that reason, a machine builder might make that roll 100 thou [thousandths of an inch] larger in diameter in the middle than at the ends. With deflection, that plate will be parallel under load, which is what we want. It gives you a nice straight sheet if you are using the material that the machine was ideally crowned for.”
Variation away from that ideal plate thickness will affect the roll. If the material is lighter gauge, that variation is going to open up the material at both ends, creating an hourglass shape in it.
“Old-school operators would manage this issue by placing cardboard in the ends or using shim stock to straighten out the problem,” said Bonnay.
The versatility of modern machinery, however, affords you with other options. If you are going to run a variety of materials, creating cans of varied diameters, a plate roller that allows you to switch out the top roll can be a useful option, particularly if you will be processing parts with a tight radius. The only challenge created by such a setup is the time required for switching out the top roll, which can be as much as 40 minutes.
If your process requires greater force on the part, it’s possible to find systems with hydraulic crowning support, allowing for a top roll that produces more force without being too large for your shop’s ideal product mix.
“We have installed systems like the one Raglan purchased recently where, if they hadn’t used this crowning technology, the top roll required would have been too large to properly roll the shapes they make,” said Bonnay. (For the full story of Raglan’s machine, check out “Managing the talent crunch at Raglan.") “And in that shop’s situation, it wasn’t very thick plate they were rolling, but very hard material that required a great deal of force.”
“Machines with rolls at shorter distance need larger hydraulic cylinders (installed forces and larger structures) to ensure the same bending capabilities, with the advantage of higher bending accuracy but with the disadvantage of requiring a higher investment,” noted Comparin.
Comparin noted, when evaluating whether to invest more in a machine with tighter geometry (closer rolls) and higher tonnage, it’s important to consider the amount of material to be cut at the edge that has not been properly rolled in the prebending phase; the time spent calibrating the circularity of the shell; and the quality expected in the final product. Some jobs definitely require more precision than others.
Consulting with a trusted supplier is key need when investing in your first plate roller. Machine builders can help hone your search for a machine that suits your shop’s needs and get you started with the right-sized model with the necessary versatility and precision.
Editor Robert Colman can be reached at rcolman@canadianfabweld.com.
DAVI Inc., www.davi.com
Faccin Group, www.faccingroup.com
Toronto, M1R 0A1 Canada
See More by Rob Colman
Robert Colman has worked as a writer and editor for more than 25 years, covering the needs of a variety of trades. He has been dedicated to the metalworking industry for the past 13 years, serving as editor for Metalworking Production & Purchasing (MP&P) and, since January 2016, the editor of Canadian Fabricating & Welding. He graduated with a B.A. degree from McGill University and a Master’s degree from UBC.
Read more from this issue
Subscribe to Canadian Fabricating & Welding
Find Canadian Fabricating & Welding on Facebook
Find Canadian Fabricating & Welding on Twitter
Keep up to date with the latest news, events, and technology for all things metal from our pair of monthly magazines written specifically for Canadian manufacturers!
Easily access valuable industry resources now with full access to the digital edition of Canadian Metalworking.
Easily access valuable industry resources now with full access to the digital edition of Canadian Fabricating & Welding.
Learn why Maine's Lyman-Morse Fabrication chose the efficiency, accuracy and quality of the XPR300 X-Definition Plasma. According to Jonathan Egan, fab shop manager, "The quality of the XPR300 cut is the very best that I’ve seen."
© 2023 FMA Communications Canada, Inc. All rights reserved.

40t Self-Aligning Welding Rotator/Turning Rolls Not yet registered? Sign up